This contains the core
components of the stage rig - mixers, MIDI matrix control, sequence
playback, SYSEX backup, and modules essential for rhythm. My
preference for line level mixers have been Rane SM82 as they are
clear
& transparent, and they can be chained as your system grows.
For sequence playback and SYSEX backup I chose the Alesis Datadisk - it
uses floppy disks but no one has made a MIDI accessory like this with
newer memory like USB sticks! Proving again that old stuff fits
the bill, I use a JL Cooper MSB+ for a programmable MIDI matrix.
Most of these are duplicates of my studio system, and I prefer to
minimize the learning curve of new devices. Since most of these
devices use external power supplies, I placed the Juice Goose 12Paq in
this rack. None of the other racks have any need for external
power supplies.
Components:
- Juice
Goose 12Paq (universal low voltage power supply, designed to
eliminate “wall warts”)
- Alesis
Datadisk (portable media MIDI backup/restore and MIDI sequence
playback)
- JL
Cooper MSB+ (programmable MIDI matrix)
- Alesis DMPro
(ROMpler sound source drums and percussion
with built in digital effects)
- Rane SM82
(line level mixer, stage monitor summing)
- Eventide 2016
(removed, no longer needed)
- I/O panel, MIDI & AC distribution
- Moog Minitaur
(analog sound source for huge Taurus pedal
sounds)
- Rane SM82
(line level mixer, main keyboard to FOH)
- I/O panel, main keyboard inputs, monitor output, & FOH
outputs
|
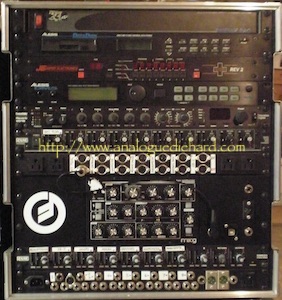
|